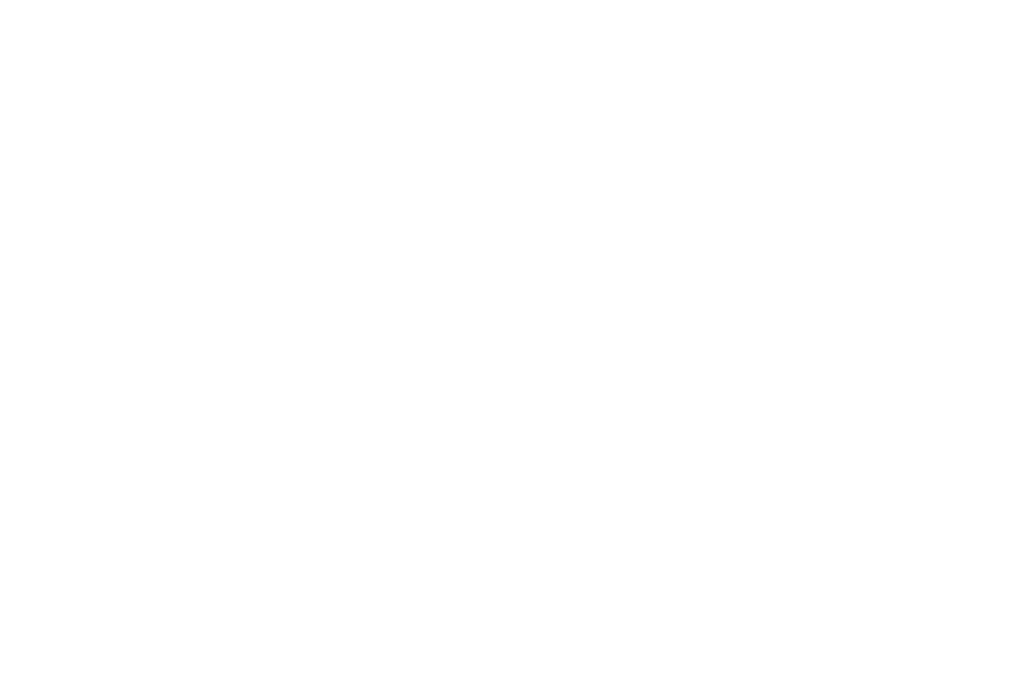
Цель проекта
Разработка по заказу и при активном участии ПАО «Газпром нефть» решения для процесс-майнинга для минимизации санкционных рисков и сведения значительного опыта исследований предметной области с современными технологиями процессного анализа на уровне лучших мировых продуктов.
Решение
В рамках проекта был разработан и продолжает развиваться программный продукт, полностью соответствующий всем требованиям бизнес заказчика, брендбука, ИТ архитектуры и информационной безопасности компании.
Для разработки «Промайн» использовались языки программирования и современные технологии с открытым кодом, обеспечивающие лицензионную чистоту продукта (MIT, Apache 2.0 и др). Математический аппарат и алгоритмы разрабатывались на основе открытых научных подходов и публикаций, а также собственных исследований.
Ключевые результаты проекта
Система введена в промышленную эксплуатацию на более чем 100 пользователей и внедрена в десятки процессов (объемом до 100 млн событий каждый) в периметре компании.
Получены значительные финансовые эффекты от снижения рисков и повышения эффективности процессов с помощью «Промайн».
Идет активное развитие функционала, включая сложные математические методы симуляции, поиска первопричины отклонения ключевых показателей процессов и автоматизации отчетности.
В сентябре 2023 ПАО «Газпром нефть» зарегистрировал собственный продукт «Промайн» в реестр российского Программного обеспечения (Минцифры) и начал продажи на рынке.
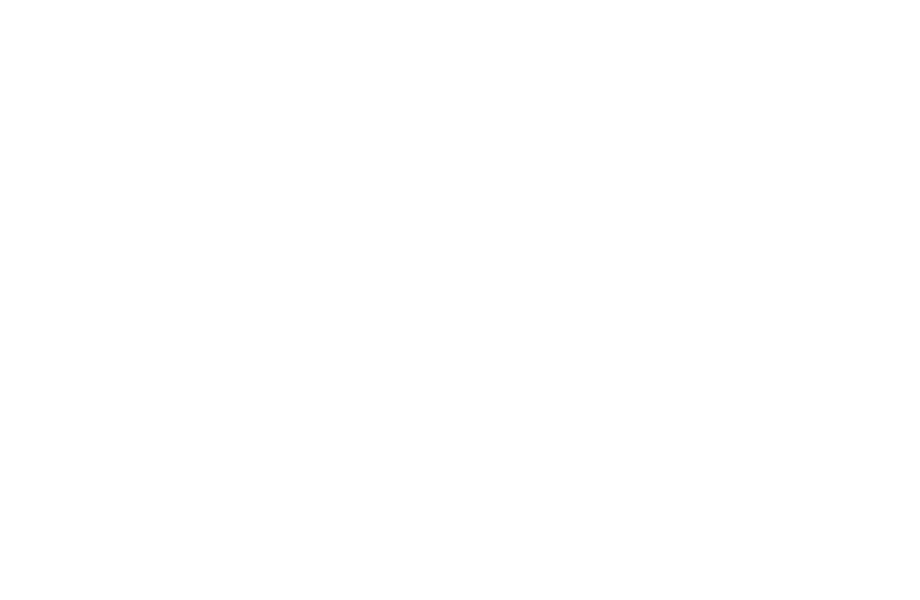
Цель проекта
Разработка цифрового двойника производства строительных блоков для крупной отечественной компании.
Решение
Разработка цифрового двойника предполагает создания точной и эффективной копии реального производственного процесса. Она позволит контролировать и оптимизировать производство, обеспечивая снижение затрат и увеличение производительности.
Цифровой двойник представляет собой виртуальную модель производственной линии, которая имитирует все этапы изготовления строительных блоков, от добычи сырья до упаковки готовой продукции. С помощью датчиков и контроллеров, установленных на реальном производстве, данные о процессе постоянно обновляются и передаются в цифровой двойник, который анализирует их и выдает рекомендации по улучшению работы оборудования и оптимизации процессов.
Решение включает в себя алгоритмы машинного обучения, которые позволяют анализировать большие объемы данных и выявлять закономерности и тенденции, которые могут быть использованы для оптимизации производства. Например, система может определить, какие факторы влияют на качество продукции, и предложить решения для их устранения.
Ключевые результаты проекта
Цифровой двойник позволил сократить время на внедрение новых технологий и оптимизировал технологический процесс и использование ресурсов и уменьшил количества брака.
Система используется для прогнозирования результатов выработки продукции, оценки возможных рисков и обеспечивает принятие обоснованных решений.